23 Pedal to the....Plywood? Guitar Pedalboard Build
- Frank Walker
- Jun 24, 2021
- 3 min read
The Design
Clearly, I had reached the point where I just wanted to fill my still-to-be-finished studio with more furniture! Shortly after building my sidecar, I decided I also needed a new guitar pedalboard. My current pedalboard was designed for lugging about gigging, it was a sturdy case but was flat and didn't have any space for hiding cables. I wanted a board that looked nice, could hide the cabling, and functionally more convenient.
I initially looked around the internet for a new board to purchase, but most didn't fulfil my needs or were too large. There were some nice designs on Etsy, but they were coming up too pricey for the likes of me and my wallet. So, as always, I turned my attention to building my own.
The first port of call was designing in AutoCad . I wanted to make sure the board wasn't any bigger than it needed to be, as I'm conscious of the lack of available space in the studio. Fortunately, I don't have too many pedals, just what I'd consider the essentials to cover the sounds I like to make. I made some extremely basic models of the pedals in AutoCad, just so I could get the dimensions down and think about the layout. I wanted the noise gate to react after the gain stage of the amplifier, as well as having the time-based effects on the send and return loop. This means, as can be seen in the diagram below, I would have two input and two output stages on the board. I roughly arranged the pedals in this pre/post amp stage, but also keeping sure I have the pedals that I turn on and off more frequently on the bottom row.

Once I had the basic size of the board, I could get into the nitty gritty of all the other measurements and angles. One key feature of the design, is that the board would be angled up, not only to help provide more space for the power supply and cables underneath, but also for ease of reaching the pedals on the back row. I would be connecting all the frames with box joints, and attaching the front panel (with cut outs for cables) with metal hinges.

The Build
As you can see below, the design changed slightly when I began making it. I moved the two handles at the side, to just one at the back, this just made better use of the limited space for connections and switches. I built this board out of birch plywood, again, staying true to form with the rest of the studio. My first attempt at a box joint below, a few chips appeared when chiselling, which I would hopefully hide by sanding down the edges.
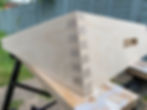
Rounding off the edges with a sander...
Finished sanded frame and top plate, pictured with studio/workshop assistant.

I needed to make a few more cuts in the plywood to mount the jack ports and power switch, these were simply down with a circular drill bit and a jigsaw. Once all the cuts had been made and all sanded down, I could go through the process of applying Danish Oil for a smooth finish.
The next stage was then attaching the fabric to the top plate, I simply cut the fabric to size and pressed down to the plywood board with adhesive spray.
Then, with a Stanley knife, I made a straight line incisions where the cut-outs in the plywood top were. Leaving just a small slit in the fabric meant all the cables and power supply beneath the board would still be hidden out of view.
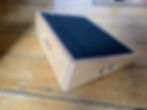
Finally, I could finish up on the little details such as wiring up the plug and jack ports, and attaching small rubber feet to the underside.
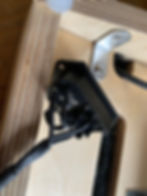
The Finished Project
And then it was ready! Pedals on and all wired up.
Thanks for reading, and let us know if you've ever made your own pedalboard or are thinking of making one! Next time, we finally go back to finishing the studio.
Frank Leonard Walker
#BasementConversion #AcousticTreatment #StudioDesign #StudioBuild #StudioPlanning #Mixing #Mastering #ControlRoom #RecordingStudio #MixingAndMastering #HomeStudio #MusicStudio #Acoustics #StudioAcoustics #KentStudio #BasementStudio #HomeStudioBuild #GuitarPedals #GuitarPedalBoard #GuitarPedalBoards #GuitarPedal